Pinch Valve Manufacturer
Our pinch valves use a flexible elastomeric sleeve as the primary sealing element, which is pinched closed by external force—either manually, pneumatically (air-actuated pinch valve), or electrically (electric pinch valve). Ideal for handling abrasive, corrosive, or high-purity materials without contamination.
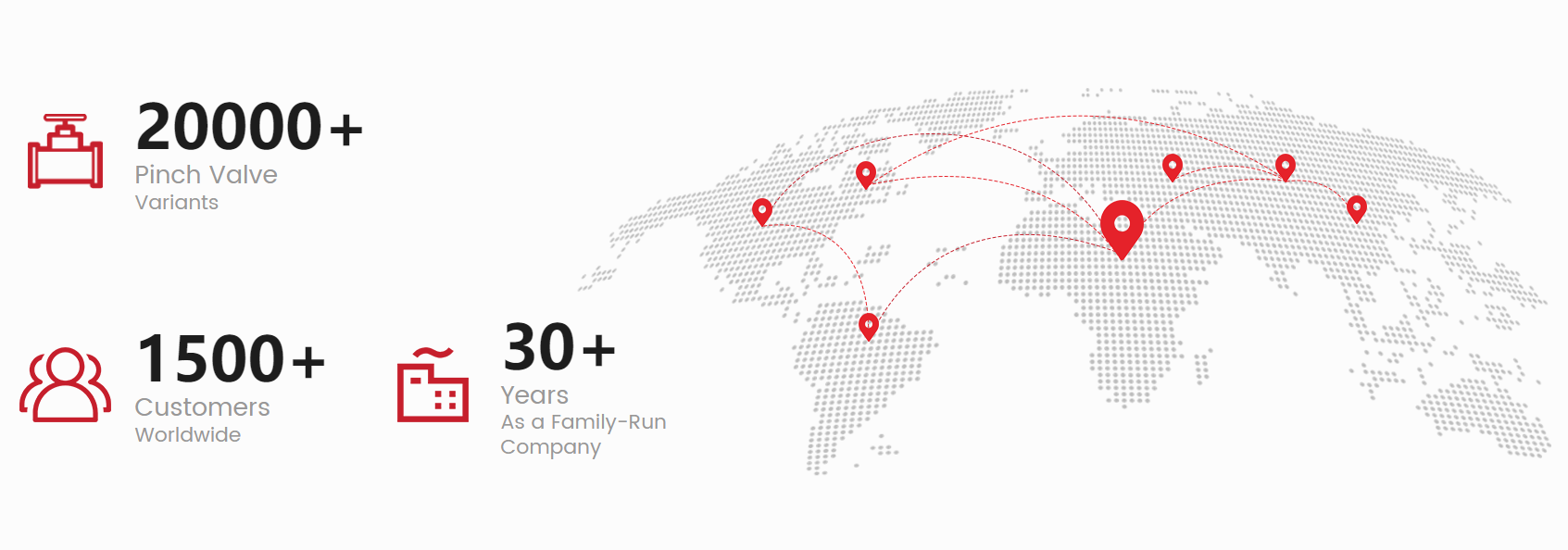
About Us
Lianke Valve Co., Ltd., originally founded at Wenzhou Yongzhong Chemical Machinery Plant in 1982, has built a legacy of innovation and quality in the valve industry.
Our primary products include pinch valves, fluorine-lined valves, and strainers. We proudly hold certifications from API, CE, ISO, and TS, ensuring our products meet global standards.
Our manufacturing processes adhere to rigorous industry standards such as API, DIN, JIS, and GB, while maintaining strict alignment with ISO9001 quality management principles.
As a trusted provider of valve solutions, we specialize in various filter types, including blue, precision, Y, and T filters, all designed with customer satisfaction at the forefront. Our commitment to excellence drives continuous innovation, allowing us to stay competitive both domestically and internationally.
We Meet the Highest Industry Standards
Our pinch valves meet rigorous industry standards and quality certifications to ensure optimal performance and safety
- EAC: Conformity with Eurasian standards for safety and quality.
- CE: Compliance with European health, safety, and environmental protection standards.
- ISO 14001: Environmental management system certification.
- ISO 9001: Quality management system certification ensuring consistent quality.
- ISO 45001: Occupational health and safety management certification.
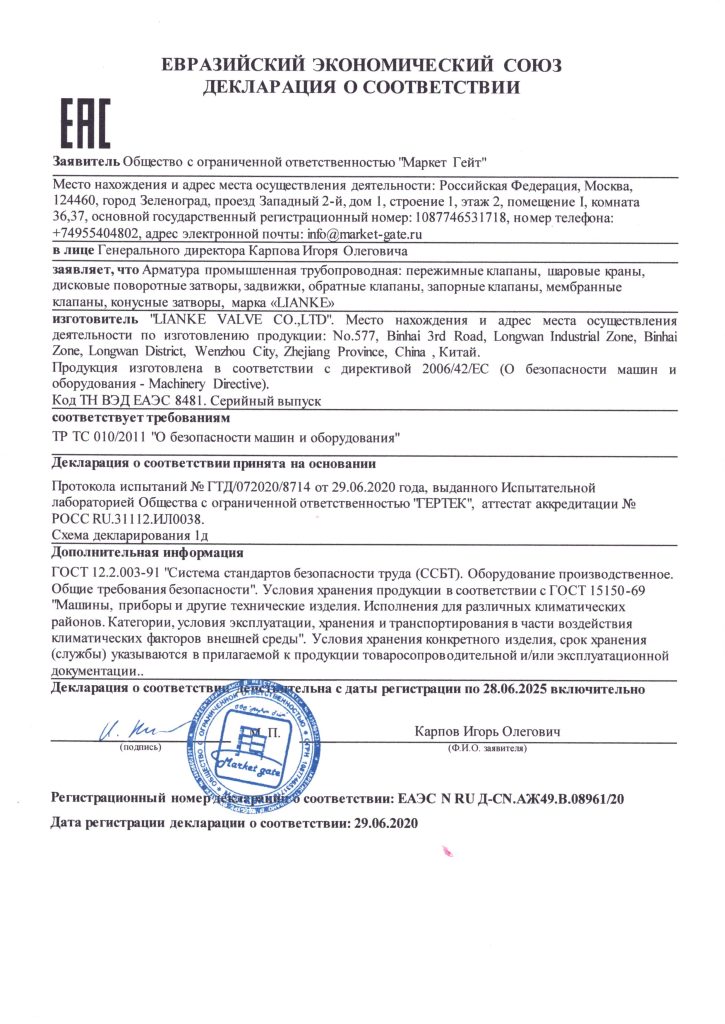
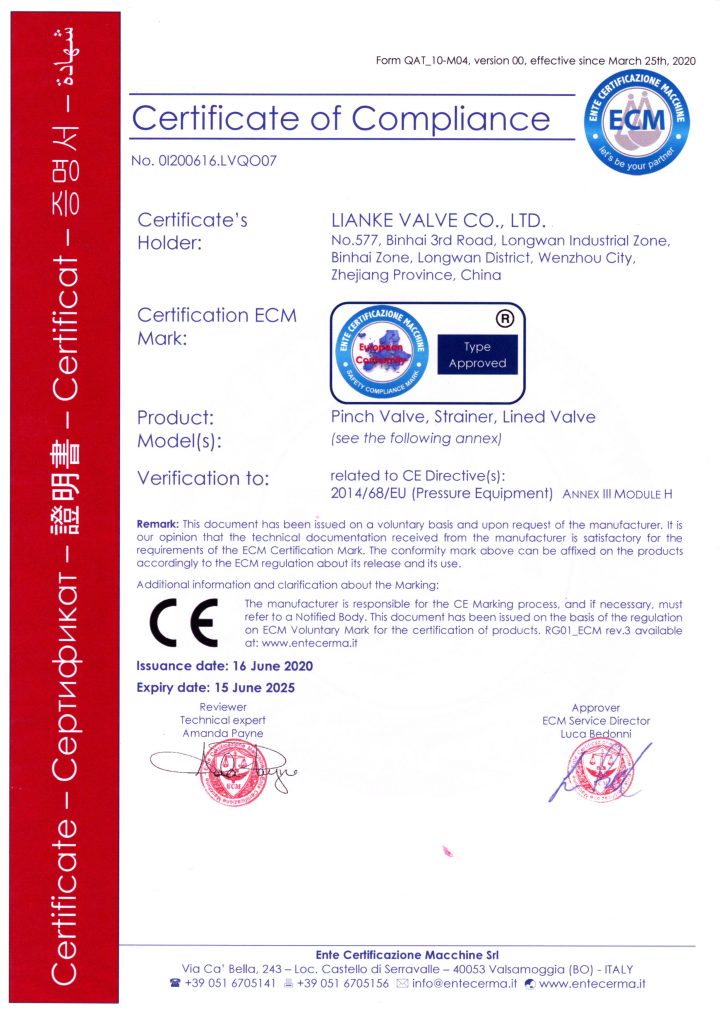
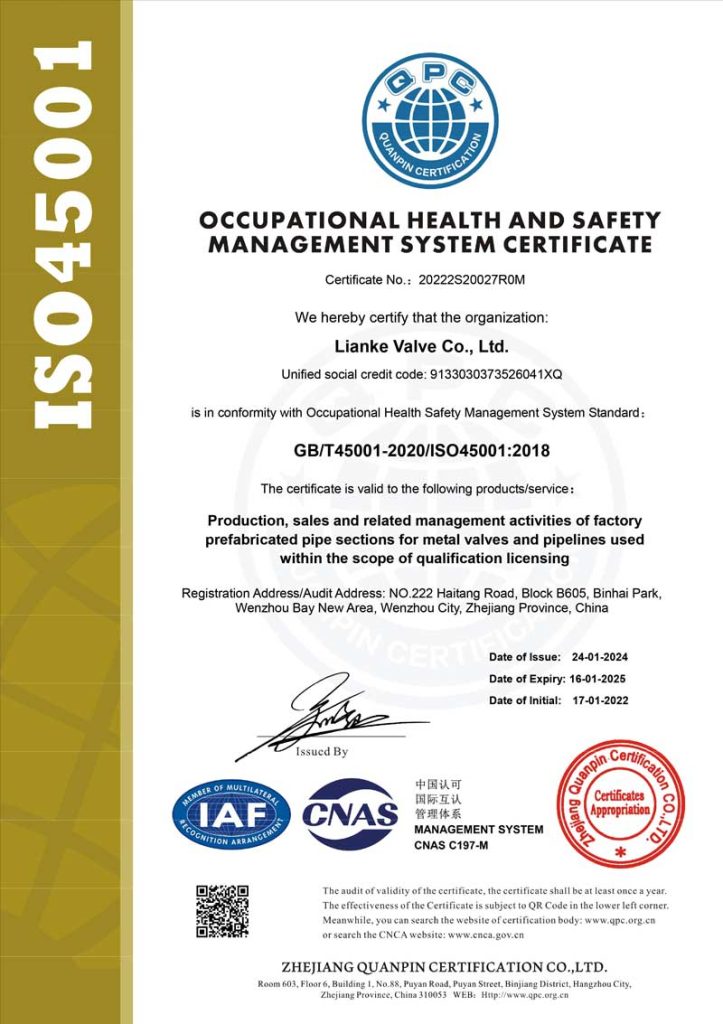
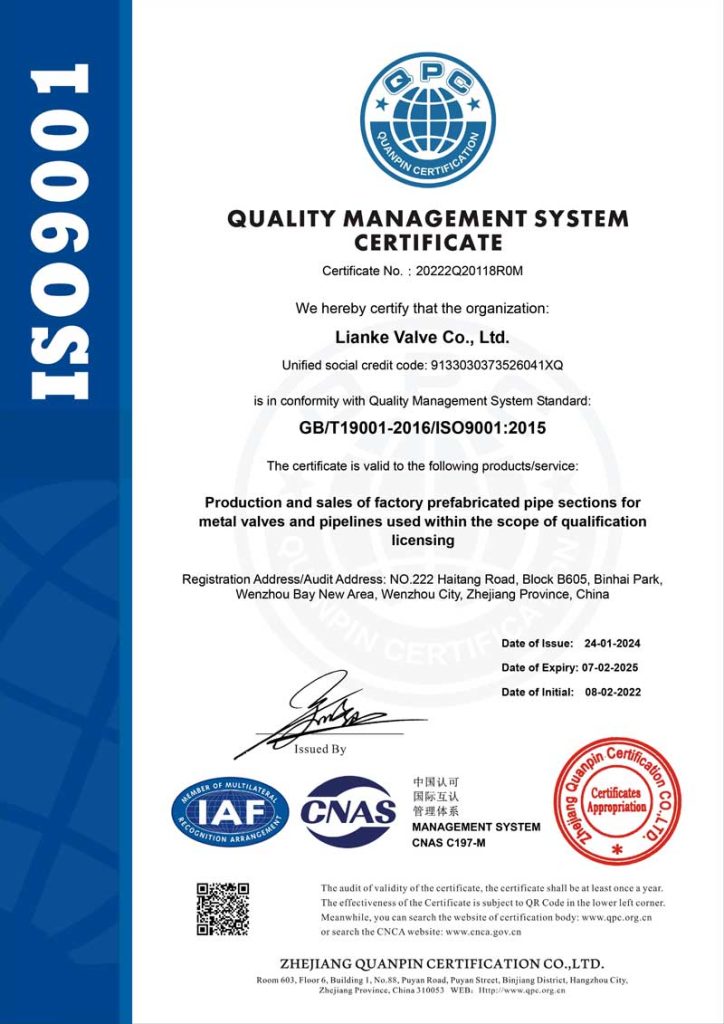
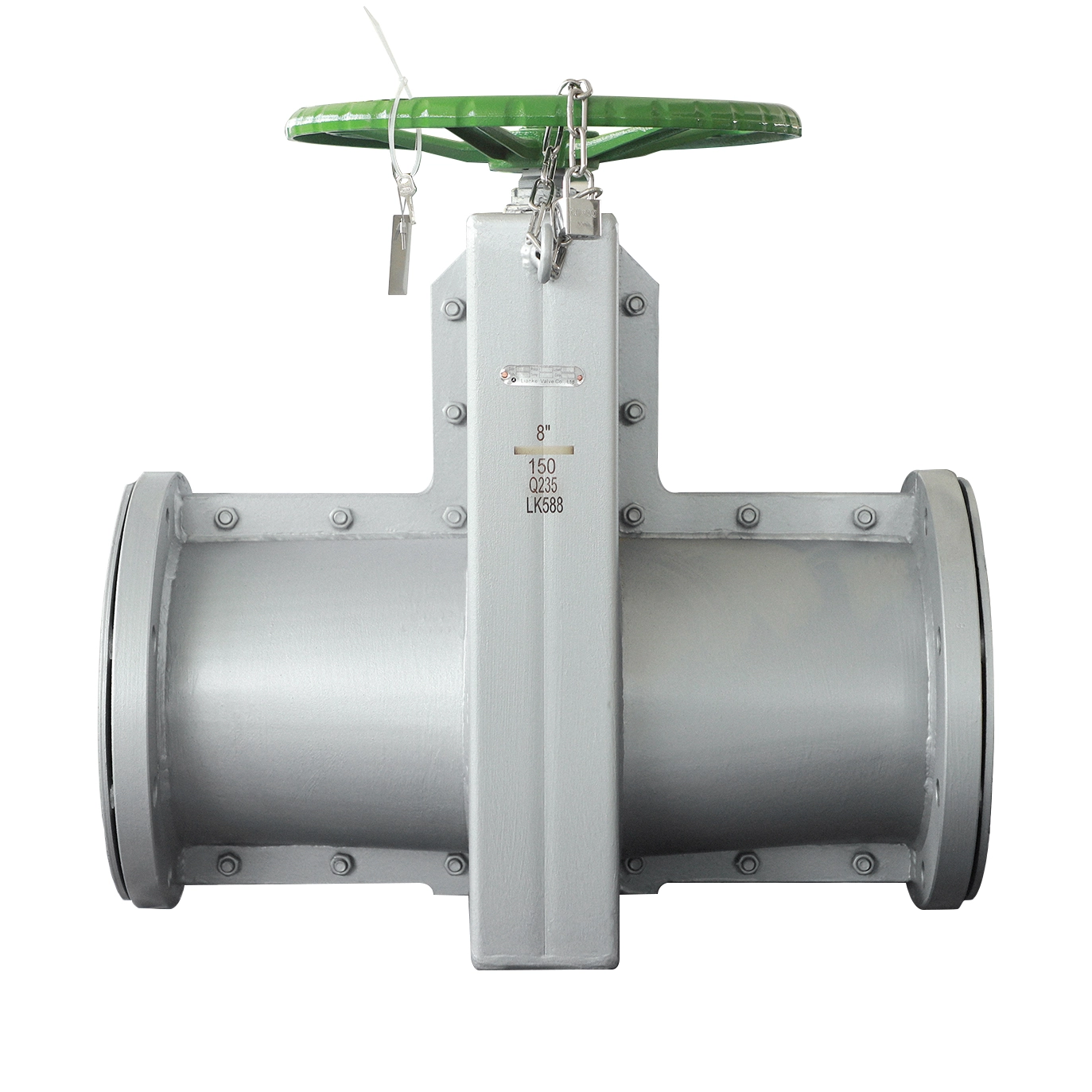
Manual Pinch Valve
Operated by a hand wheel to lower a pinch bar that compresses the sleeve, stopping the flow. Featuring a lock to prevent unauthorized operation, secures the valve position against accidental movement and ensures consistent control over fluid flow in various applications
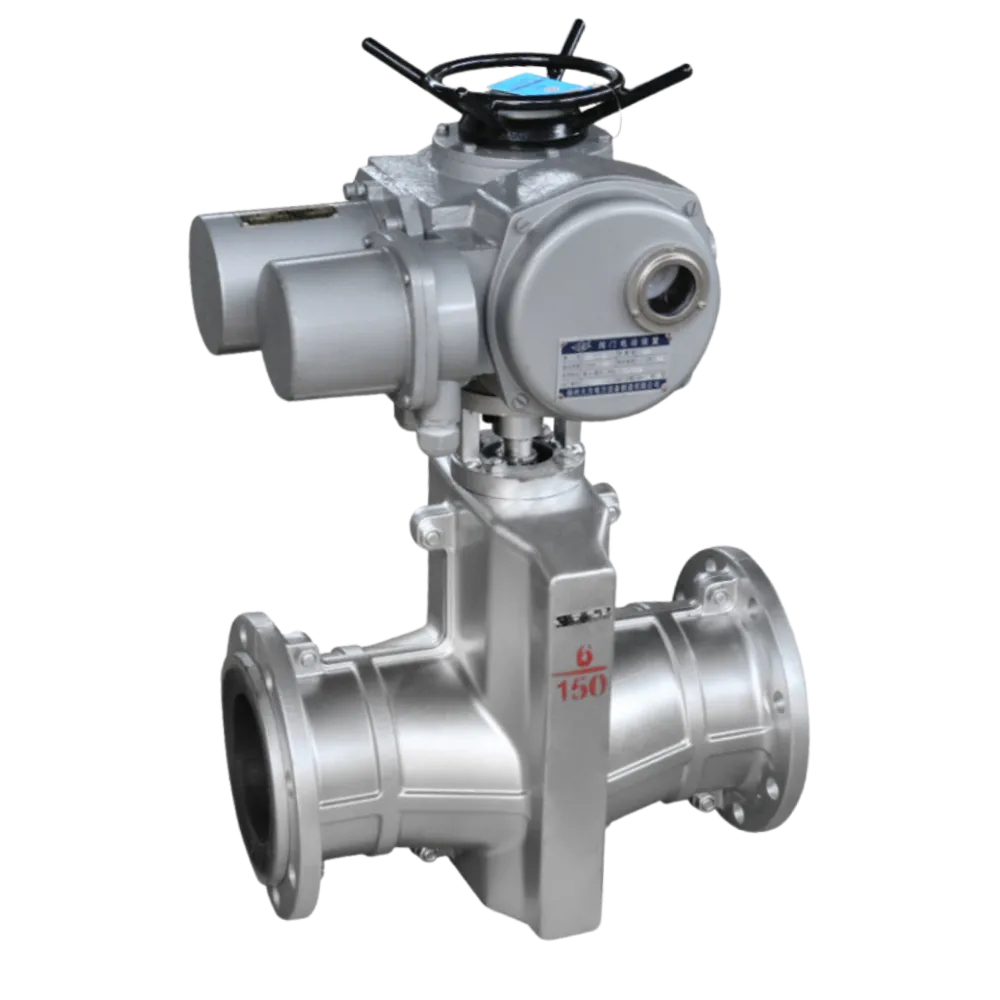
electric Pinch Valvel
Operated efficiently with electric actuators, offering options for manual override. Its design allows for quick tube changes and self-cleaning capabilities. With a wide temperature range and high-pressure tolerance, suitable for wastewater treatment and pharmaceuticals.
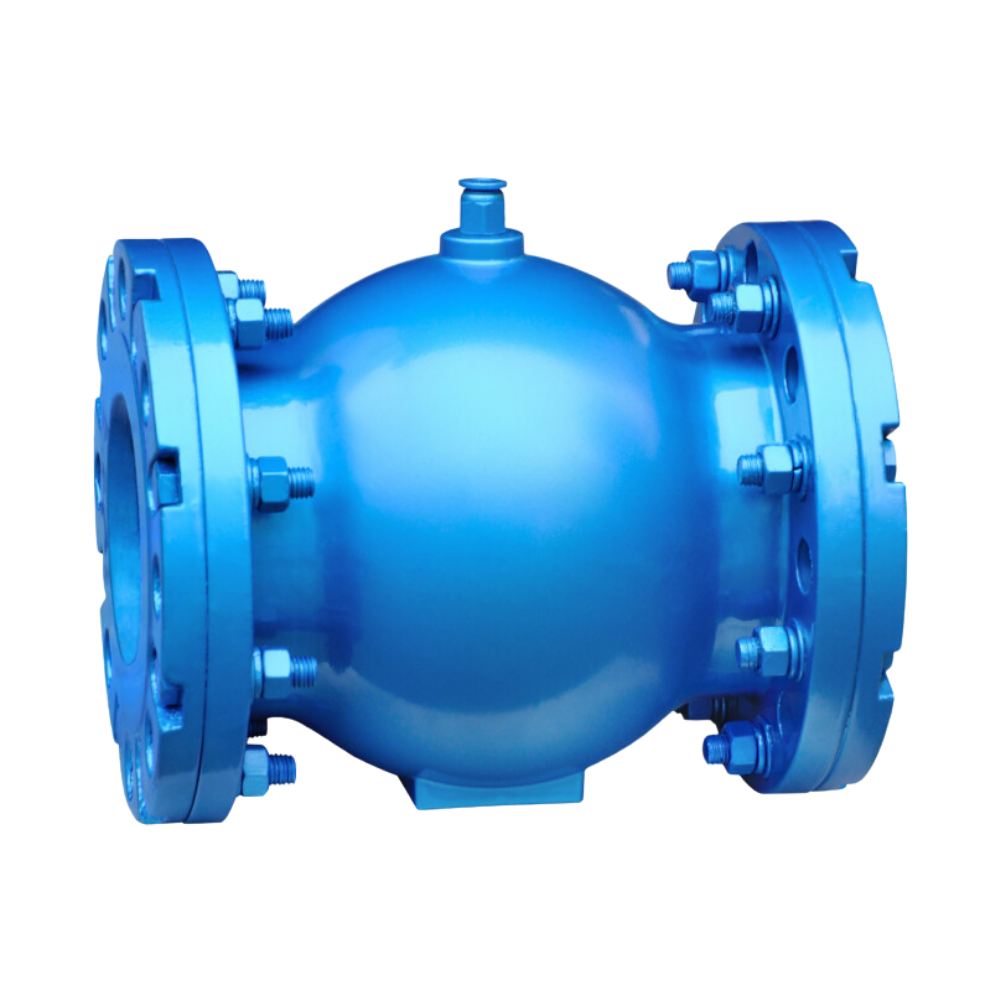
air-actuated Pinch Valve
This Valve utilizes an air-actuated mechanism to compress a flexible rubber sleeve, featuring EPDM, NR, NBR, CR, and IIR, with a temperature range of -40 to +110°C. Available in DN 40-300 and PN 1-16.
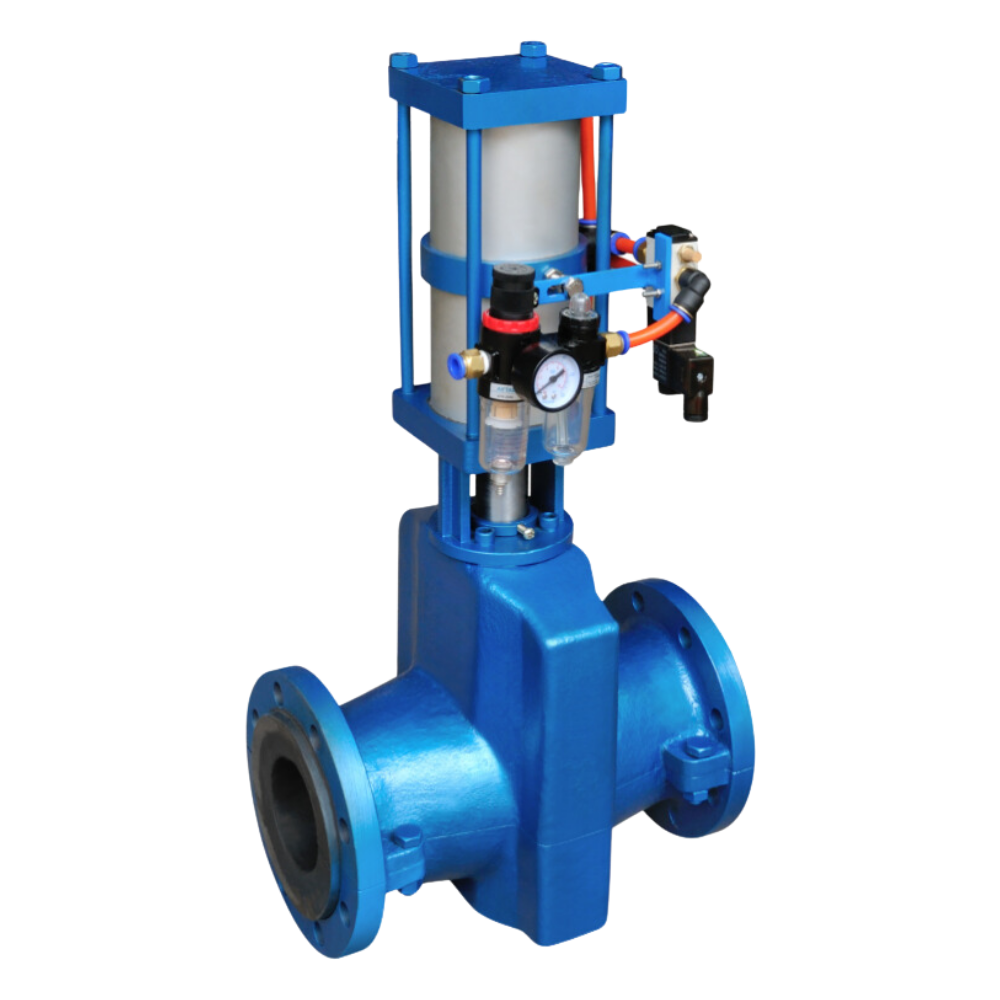
pneumatic pinch valve
uses compressed air to control the flow of gases or liquids, enabling precise flow regulation in automated and industrial systems. It offers quick, reliable operation with low energy consumption
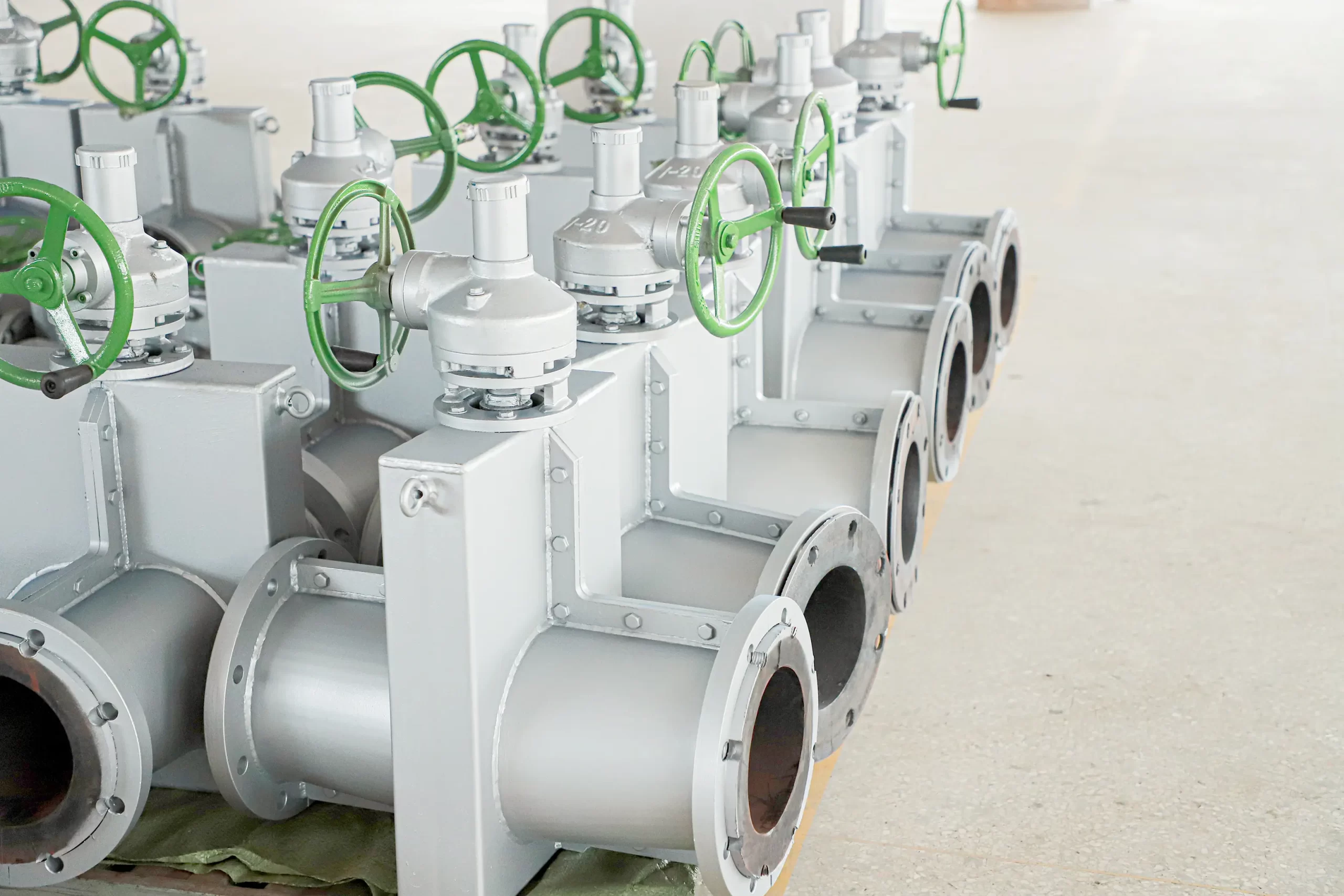
How do pinch valves work?
In operation, external force—either mechanical or pneumatic—is applied to “pinch” the sleeve, creating a seal that stops the flow. For pneumatic pinch valves, pressurized air is introduced into the housing, compressing the sleeve and closing the valve. When the air pressure is released, the elasticity of the rubber sleeve and the force of the flowing media restore it to its open position. Mechanical pinch valves achieve this effect manually via a handwheel or through hydraulic mechanisms.
Frequently Asked Questions (FAQ)
Pinch valves are ideal for handling slurries, powders, and abrasive media in industries including: Mining and mineral processing, Wastewater treatment, Food and beverage, Chemical processing, Pharmaceutical manufacturing
- Our pinch valve sleeves are available in:
- Natural rubber
- EPDM
- Neoprene
- Nitrile (NBR)
- Hypalon
- Butyl
- Viton/FKM
Our pinch valves are available in sizes ranging from 1/2″ (DN15) to 24″ (DN600), with custom sizes available upon request.
We offer multiple actuation options:
- Manual handwheel
- Pneumatic (single or double acting)
- Electric actuator
- Hydraulic actuator
Key benefits include:
- Full bore design with no flow restrictions
- No cavities where material can accumulate
- Simple maintenance with minimal parts
- Cost-effective for abrasive applications
- Self-cleaning design
- Excellent throttling capabilities
The sleeve life depends on service conditions, but typically ranges from 1-5 years under normal operation. Factors affecting sleeve life include:
- Media characteristics
- Operating temperature
- Cycling frequency
- Operating pressure
- Environmental conditions
Maintenance requirements are minimal:
- Regular visual inspection of the sleeve
- Periodic checking of actuator operation
- Sleeve replacement when worn
- No lubrication required
- No packing adjustment needed
- Operating pressure: Up to 145 PSI (10 bar)
- Temperature range: -4°F to 266°F (-20°C to 130°C)
- Custom designs available for higher pressure/temperature requirements
- Temperature limits vary by sleeve material selection
- Pressure ratings depend on valve size and application
Key selection criteria include:
- Media characteristics (abrasiveness, corrosiveness, viscosity)
- Operating conditions (pressure, temperature, cycling frequency)
- Process requirements (flow rate, control needs)
- Installation environment
- Required certifications
- Budget considerations