Lined Wafer Butterfly Valve
Lined Globe Valve
Lined Ball Valve
GB/T12221 ASME B 16.10
Lined Diaphragm Valve
Lined Gate Valve
corrosion resistant lined valve collection
Innovate Technology
At Lianke, we stay at the forefront of innovation, employing advanced computer simulation analysis technology for our product design, resulting in superior performance and efficiency.
Quality Control
With our CE, ISO9001, ISO14001, OHSAS18001, and API certifications, we prioritize stringent quality control measures, ensuring each valve meets the highest industry standards and giving you confidence in its reliability
Safe and Reliable
Rest assured with our comprehensive testing procedures, where each order undergoes 4 or more test reports, guaranteeing the utmost safety and dependability of your entire project system
Wide Range of Products
Our diverse portfolio encompasses a wide selection of lined valves, catering to various industrial needs and applications.
Best Price
While delivering uncompromising quality, we offer competitive pricing, ensuring you receive the best value for your investment in our top-notch products
Corporate Responsibility
Beyond profits, we embrace our responsibility towards society, striving to create more value through sustainable practices and initiatives, making a positive impact on the community and the environment
We Are Here to Answer All Your Questions
Here are some frequently asked questions about Lianke Lined Valve
What is the purpose of valve lining?
Valve lining protects against corrosive media, prevents contamination, and extends service life of lined valves. This protective barrier ensures product purity while reducing maintenance costs in industrial applications.
Which lining materials are commonly used?
Common lining materials include PTFE lined valves, PFA lined valves, FEP lined valves, PP lined valves, and PVDF lined valves. Each offers specific chemical resistance and performance benefits.
How long does valve lining typically last?
PTFE/PFA lined valves typically last 8-12 years, while PP/PVDF lined valves serve 5-8 years. Lifespan depends on temperature, chemical exposure, cycling frequency, and maintenance quality.
When should lined valves be replaced?
Replace lined valves when showing lining damage, connection leaks, irregular operation, chemical contamination, or loss of corrosion resistance. Regular inspection prevents unexpected lined valve failures.
Get A Quote Now
Get in touch with LIANKE VALVE GROUP CO LTD now to purchase your Lined Valve and ensure reliable fluid control.
Application
Lined valves are essential in chemical processing for corrosive media handling, pharmaceutical manufacturing for ultra-pure systems, water treatment facilities, metal processing industries for acid applications, and pulp/paper production. These valves protect against corrosion while maintaining process integrity in aggressive chemical environments.
- Chemical Processing
- Pharmaceutical Industry
- Water Treatment
- Metal Processing
- Pulp and Paper
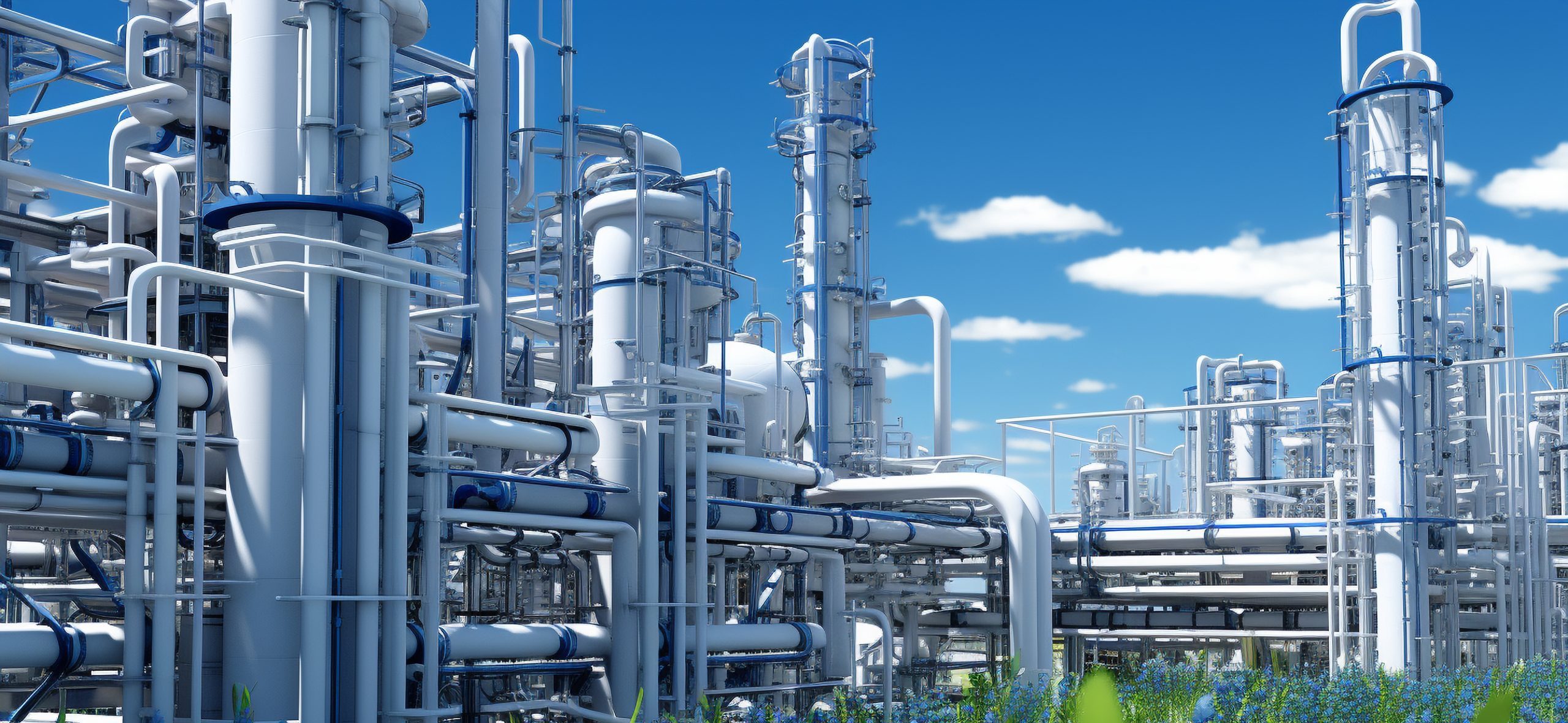
PTFE and PFA-Lined Valves: Which is the Best?
Defining PTFE and PFA
Before diving into the comparison, it’s essential to understand what PTFE and PFA are.
PTFE, commonly known under the brand name Teflon®, is a synthetic fluoropolymer of tetrafluoroethylene.
This material is widely used for its non-stick properties and resistance to high temperatures and chemicals.
On the other hand, PFA is a copolymer of hexafluoropropylene and perfluoro ethers, also marketed as Teflon® PFA.
PFA shares many of the same properties as PTFE but has a different molecular structure, allowing it to be processed through conventional injection molding techniques.
PTFE-Lined Valves
A PTFE-lined ball valve is popular for applications that involve corrosive or aggressive chemicals, particularly in industries like chemical processing and pharmaceuticals.
PTFE’s non-reactive properties make it highly resistant to acids, bases, and solvents, which ensures the long life of the valve components.
In ball valves, a PTFE lining ensures that the media in the pipeline doesn’t come into contact with the valve’s metal parts — reducing the risk of corrosion and contamination.
However, one drawback of PTFE is that it cannot be injection molded, which can lead to imperfections such as pinholes during the manufacturing process.
These pinholes may compromise the integrity of the valve when exposed to certain chemicals over time.
Similarly, a PTFE butterfly valve offers excellent chemical resistance and can operate effectively in high-temperature environments.
These valves are often used in industries handling volatile substances. However, PTFE-lined valves, including Teflon-lined ball valves and Teflon-lined butterfly valves, may experience cold flow—deformation under constant pressure—which can limit their use in high-pressure environments.
PFA-Lined Valves
In comparison, PFA-lined ball valves offer the same heat and chemical resistance as PTFE but with added benefits due to their unique processing capabilities.
Unlike PTFE, PFA can be injection-molded, allowing for a smoother, more uniform lining inside the valve.
This process ensures that PFA-lined ball valves have better resistance to permeation — making them ideal for applications requiring long-term durability and safety.
Additionally, because PFA can be molded to a higher precision, it is less likely to develop pinholes, which enhances its performance in highly corrosive environments.
When it comes to abrasive process conditions, PFA outperforms PTFE. For instance, in the pulp and paper industry, where slurries and corrosive substances are common, the thickness of the PFA liner can be increased along the edges of the valve, providing enhanced abrasion resistance.
This is particularly true in lined ball valves used in slurry and abrasive applications.
In contrast, PTFE tends to delaminate or wear down faster under similar conditions, especially at the edges where the liner is bonded.
Key Advantages of PFA Over PTFE
The flexibility of PFA as a material allows manufacturers to create more complex and resilient valve linings compared to PTFE.
For example, the injection molding process used for PFA ensures a more secure bond between the lining and the valve body.
This helps prevent delamination under negative pressure, a situation where PTFE-lined valves, such as PTFE-lined butterfly valves, may fail.
Furthermore, PFA’s smooth surface reduces the chance of process fluids penetrating the liner and reaching the valve’s metal parts, enhancing the valve’s longevity.
Another advantage of PFA is its superior permeation resistance.
In some industrial applications, even trace amounts of permeation can lead to contamination, which may be catastrophic in industries like semiconductor manufacturing.
PFA, particularly the Super PFA variety, provides much better protection against permeation than PTFE.
For instance, tests have shown that PFA can offer up to three times the permeation resistance of PTFE when exposed to corrosive substances like hydrochloric acid.
Applications of PTFE and PFA-Lined Valves
Both PTFE and PFA-lined valves are extensively used in industries where chemical resistance is crucial.
A Teflon butterfly valve or a PTFE-lined ball valve is often found in chemical processing, water treatment, and pharmaceutical industries, where durability and non-reactivity are essential.
Meanwhile, PFA-lined ball valves are frequently used in more aggressive environments, such as semiconductor manufacturing or chemical plants, where the risk of permeation and abrasion is higher.
Another commonly used valve type in these industries is the lined plug valve, which can be lined with either PTFE or PFA, depending on the application’s specific needs.
Teflon-lined valves are preferred when dealing with less abrasive media, whereas PFA-lined valves are better suited for more demanding applications, such as handling slurries or highly corrosive chemicals.